Table of Content
Walls are poured around the perimeter to be even with or slightly higher than ground level. The advantage of a pit-set foundation is that you get a much largercrawl space. You now know what it takes to install a new mobile home anchor which should now be situated slightly under the home. Clear of the skirting and in line with the overhead strap attachment on the home or shed. Hard rock anchors, as you may guess, insert into hardened rock foundations.
Insert the anchor shaft into the hole then turn the anchor all the way down into the ground. Backfill the hole, connect the hook to the beam, connect the strap to the anchor head and finally tighten the split bolt. In this configuration, the connecting straps stretch over the roof, wrapping around the entire structure and linking it into a ground anchor on either side.
Step 3: Determine soil type
For that reason, many homeowners are upgrading their anchors to the new standards which have proven to be quite successful in recent years.
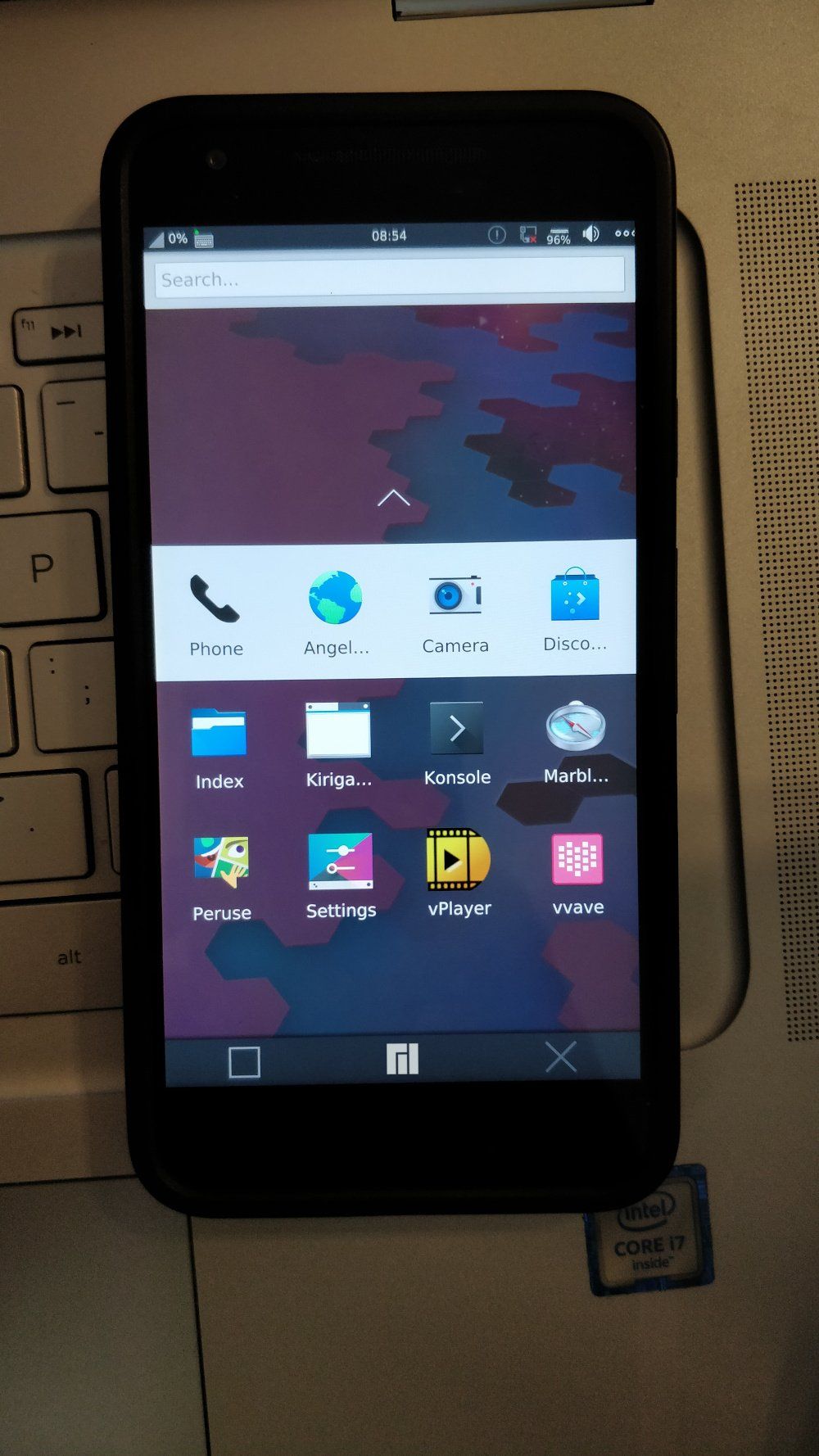
You’ll need a crane to position the home if you’re using basement foundations. Remove packing materials that protected the home during shipping. Inspect the home and all provided materials, appliances and equipment immediately upon delivery.
Window Components
You’re ready to have the mobile home installed on your home site. If everything goes well, you’re just a few short weeks away from moving into your new home. Now take the shovel fill in the top of the hole taking care to tamp down the soil every 6 inches or so to make sure that the ground is compacted and firm. This is really important, if not done correctly, the anchor will start to pull out of the ground as the split bolt is tightened up. Using your post hole diggers, start to dig your hole so that the bottom of the hole will be at an angle of 15 degrees towards the home. Dig down approximately 2 feet removing the excess dirt as necessary.

Traditional models tend to feature flat sides and ends and are built on frames. Almost all manufactured homes are elevated, situated on top of some sort of pier or foundation system, as previously mentioned. Strong, storm-force winds have the possibility of getting under the home and lifting it from the frame. In addition, the wind passing over the top of the manufactured home can create an uplift force.
Mobile Home Pest Control Tips and Tricks
Write down the steps for installation with a timeline for finishing important tasks. This ensures that the work is done in a timely and correct fashion. Next, you will need to turn the anchor in a clockwise direction applying some constant pressure with your body weight in a downward direction as you turn.
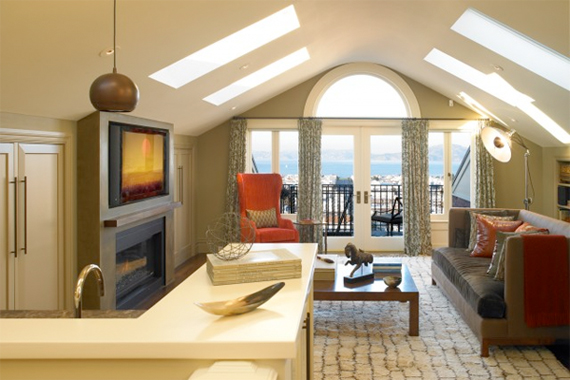
Fasten or “marry” each section together per manufacturer’s instructions and HUD codes. For example, if you’re moving into a park homes community, there probably isn’t a great deal to do beyond setting up your home and hooking up to the existing utilities. The community manager will probably take care of site preparation. So you’ve found a mobile home dealer you are comfortable with, bought your home on a square deal, found a site, and checked the zoning laws.
Anchors & Tiedowns
Hidden problems with the downspouts or grading, for example, could cause massive water ingress leading to warping and buckling sometime down the road. A faulty foundation could cause the home to settle unevenly and might have to be completely rebuilt if it isn’t up to the job. For several days or weeks your home site has looked like a chaotic building site, now everything comes together and your home is nearly ready for you. There’s just one final stage of the process to make sure that your home meets the many technical and regulatory aspects of an installation. Using a combination of hydraulic jacks, rollers and winches, move the section into its final position and remove the running gear.
New anchors will be Installed to meet your current codes for mobile homes. Determining the required number of anchors recommended for the home’s wind zone. For installing an over-the-top tie-down, place the strap on the rafter of the roof.
In recent years after major hurricane damage, the position and number of anchors used on mobile homes has changed. Presently a small doublewide home will need around 24 anchors spaced at 5′- 4″ inch intervals along the side walls. Mobile home anchors are part of the overall tie-down system designed for mobile home safety.
Longitudinal stabilizers are installed to protect your mobile home in high winds. We will then secure the turnbuckle to the end of the anchor and turn the turnbuckle adjustment until the strap is tight. Turning the rod tightens the tension on the mobile home strap. “Mobile Home Tie downs will Stabilize and protect your mobile home with mobile home. When properly installed they’ll protect your home during storms and keep your mobile home level. “Deadman” or J-hook anchors are set into wet concrete, providing a firm connection as it dries.
Constitutes the overwhelming majority of the contiguous United States and most of Alaska. Homes in this area should be rated to withstand winds of approximately 70 mph. Single-wide mobile homes, regardless of length, will require two vertical ties per side and three 3-5 diagonal ties. For a vertical tie-down, the anchor will be installed vertically. A stabilization device might also be attached to the top of the anchor and buried in the ground. In most states, the county inspector is required to make an inspection and verify that the installation meets state minimum requirements.
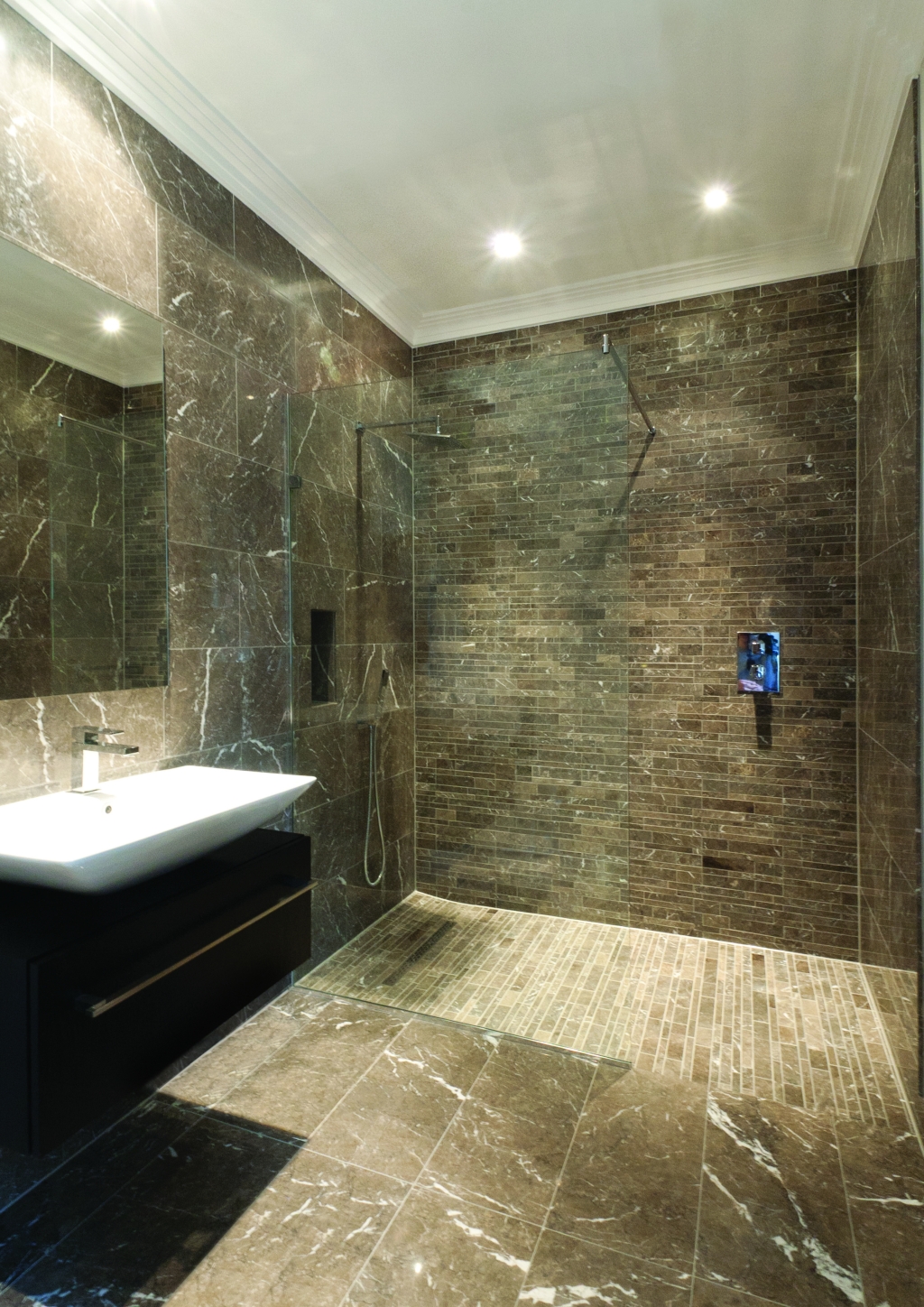
To resist wind forces, you need two different types of tie-downs. In older homes, a vertical or over-the-top tie-down is needed to compensate for the uplift force. A diagonal or frame tie-down is needed to compensate for both lateral and uplift forces. Singlewide manufactured homes need both types of tie-downs. Underhome Armor will determine which type of mobile home tie down and straps are required in your area. For a frame/diagonal tie-down, the anchor can be installed to the same angle as the tie-down.
Extra Anchors.
If the tie-down is fastened to a ground anchor with a drop-forged turnbuckle, the turnbuckle should be ½ inch or larger galvanized steel. The turnbuckle should have forged or welded eyes, not hook ends. A professional installer or “set-up” company may also offer site preparation services.
You might be able to do some of the site-preparation work yourself to reduce costs, for example, removing shrubs and trees. However, most site preparation work requires a professional and should be built into the quote from your installer or GC. Take care when doing any preparation work yourself, as mistakes could do damage to your home that’s not covered by the manufacturer’s warranty. A reputable mobile home dealer can provide you with a list of recommended general contractors and HUD-certified set-up contractors to help get your home completed on site and ready for occupancy.
No comments:
Post a Comment